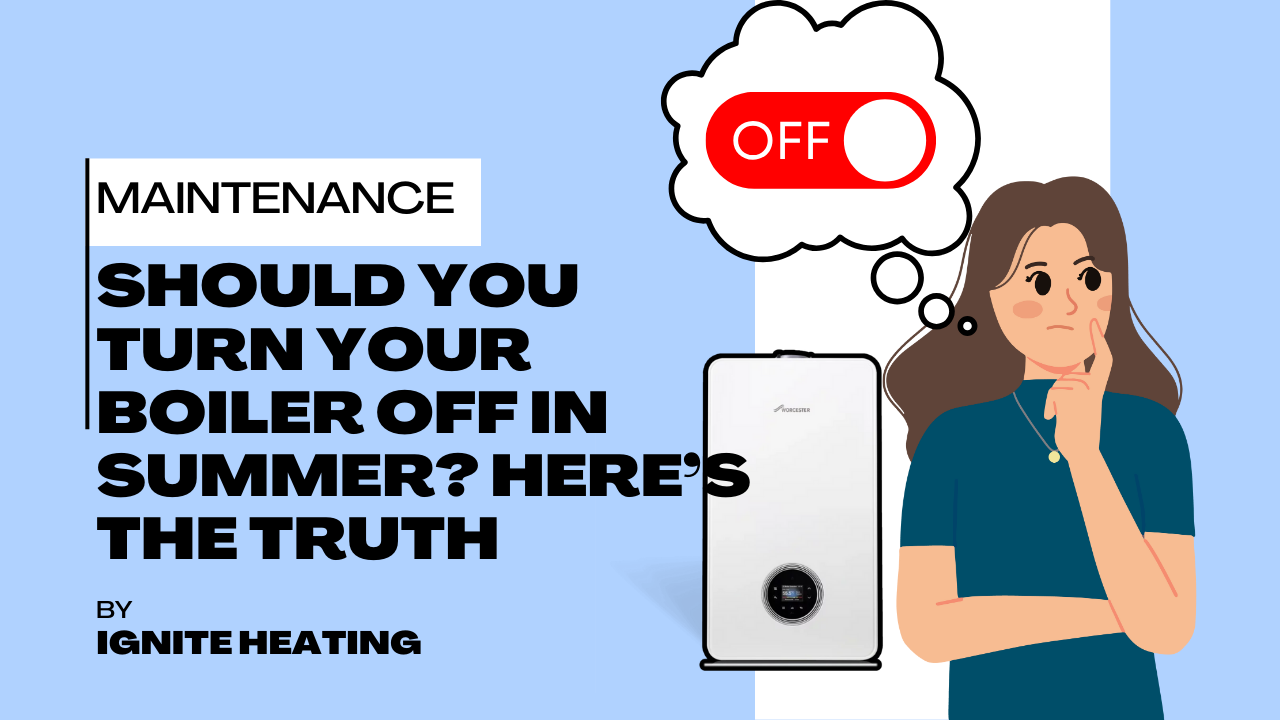
Should You Turn Your Boiler Off in Summer? Here’s the Truth.
Search Should You Turn Your Boiler Off in Summer? Here’s the Truth. Summer’s here finally. The sun’s shining (most days),
A flashing blue light on your Worcester boiler can be concerning, especially if you’re left without heating or hot water. This issue typically indicates a problem with the boiler’s ignition or gas supply. In this guide, we’ll explore the common causes, possible fixes, when to call a professional, and how to prevent future problems.
A flashing blue light on a Worcester boiler is often linked to error codes, such as EA or E9, depending on the model. These codes indicate specific faults that may prevent the boiler from operating correctly. Understanding the root causes can help you identify whether a simple reset is needed or if professional intervention is required. Here are some of the most common causes:
Ignition Failure – The boiler relies on a functioning ignition system to light the burner and produce heat. If the ignition system fails, the boiler may attempt multiple restarts before shutting down and displaying a fault code. Causes include a faulty ignition electrode, a blocked burner, or worn-out spark electrodes. This issue often requires a Gas Safe engineer to inspect and replace any defective components.
Gas Supply Problems – The boiler needs a steady gas supply to function. If the gas pressure is too low, or there is an issue with the gas meter, regulator, or supply line, the boiler may not ignite properly. External factors, such as gas network maintenance or a closed gas valve, could also be responsible. If you suspect a gas supply issue, avoid tampering with the system and call your gas supplier or a registered engineer.
Frozen Condensate Pipe – During cold weather, the external condensate pipe can freeze, blocking the flow of condensate water. This blockage causes the boiler to shut down as a safety measure. Signs of a frozen pipe include gurgling noises and error codes related to ignition failure. To fix this, you can gently thaw the pipe using warm water or insulation, but if the problem persists, an engineer may need to adjust the pipework to prevent future freezing.
Flame Detection Issues – The boiler’s flame sensor ensures that a steady flame is present during operation. If the sensor is dirty, misaligned, or faulty, it may fail to detect the flame, causing the boiler to shut down for safety reasons. A professional can clean or replace the flame sensor if necessary.
Blocked or Faulty Flue – The flue is responsible for expelling harmful gases from the boiler. If the flue is blocked by debris, ice, or an incorrectly installed pipe, the boiler will detect poor ventilation and shut down to prevent carbon monoxide buildup. Additionally, cracks or leaks in the flue can trigger safety shutdowns. A Gas Safe engineer should inspect and clear any flue obstructions to restore normal operation.
Faulty PCB (Printed Circuit Board) – The PCB is the brain of the boiler, controlling various functions, including ignition, temperature regulation, and safety features. A faulty PCB may cause intermittent errors, complete system failures, or unresponsive controls. If resetting the boiler does not resolve the flashing blue light, a professional may need to test and replace the PCB if necessary.
Understanding these common causes can help homeowners troubleshoot minor issues while knowing when to seek professional assistance. If your boiler displays a persistent flashing blue light, it is always best to consult a Gas Safe engineer to ensure a safe and effective repair. A flashing blue light on a Worcester boiler is often linked to error codes, such as EA or E9, depending on the model. Here are some of the most common causes:
Ignition Failure – The boiler is struggling to ignite, often due to gas supply issues, faulty ignition components, or a blocked burner.
Gas Supply Problems – A disruption in the gas supply, low gas pressure, or issues with the gas meter can prevent proper ignition.
Frozen Condensate Pipe – During cold weather, the condensate pipe may freeze, causing blockages that lead to ignition failures.
Flame Detection Issues – A malfunctioning flame sensor may fail to detect the flame, triggering a safety shutdown.
Blocked or Faulty Flue – If the flue is blocked or has a defect, the boiler may shut down as a safety measure.
Faulty PCB (Printed Circuit Board) – The boiler’s main control board may be faulty, preventing proper operation.
Worcester boilers display specific error codes to indicate what’s wrong. Two common error codes associated with a flashing blue light are:
The EA error code signifies an ignition failure, which means the boiler has attempted to ignite but has been unsuccessful.
This is usually caused by gas supply issues, a blocked flue, or a faulty ignition system.
How to Fix:
Ensure your gas supply is active.
Reset the boiler and see if the issue persists.
Check for flue blockages.
If the problem remains, contact a Gas Safe engineer.
The E9 error code indicates an overheat fault, which means the boiler has detected excessively high temperatures.
This can be caused by a faulty pump, a blocked heat exchanger, or an airlock in the system.
How to Fix:
Turn off the boiler and allow it to cool.
Check the system pressure and top it up if necessary.
Bleed the radiators to remove airlocks.
If the issue persists, call a professional to inspect the boiler’s components.
Before calling an engineer, you can try these basic troubleshooting steps:
Reset the Boiler – Most Worcester boilers have a reset button. Hold it for about 5 seconds and wait for the boiler to restart.
Check the Gas Supply – Ensure your gas meter is working and other gas appliances are functioning.
Thaw a Frozen Condensate Pipe – If it’s cold outside, your condensate pipe may be frozen. Pour warm (not boiling) water over it to thaw any ice.
Inspect for Blockages – Check the external flue for any obstructions like debris or ice.
Ensure Power Supply – Make sure the boiler is receiving power and hasn’t tripped the fuse board.
If the flashing blue light persists after trying these steps, it’s best to call a professional.
Some boiler issues require a Gas Safe registered engineer. While some basic troubleshooting steps, like resetting the boiler or checking for frozen pipes, can be done safely, more complex issues should only be handled by a qualified professional. Attempting to repair a gas boiler without the necessary expertise can be dangerous and may even be illegal in some cases. Here’s why calling a Gas Safe engineer is essential:
Boilers are complex appliances that involve high-pressure water, gas, and electrical components. Attempting DIY repairs without the proper knowledge can lead to serious hazards, including:
Gas leaks – Incorrect handling of gas components can lead to dangerous leaks.
Carbon monoxide poisoning – Poorly executed repairs can cause deadly carbon monoxide leaks.
Electrical hazards – Boilers have intricate wiring, and tampering with electrical components without expertise can result in shocks or short circuits.
Voiding warranties – Most manufacturers require repairs to be carried out by qualified engineers to maintain warranty coverage.
Legal implications – In the UK, it is illegal for anyone who is not Gas Safe registered to work on gas appliances.
For safety and peace of mind, always contact a Gas Safe registered engineer when facing boiler issues. Their expertise ensures that your boiler is repaired safely and efficiently, keeping your home warm and secure. You should call a professional if:
The boiler won’t restart after a reset.
You suspect a gas supply issue.
There’s a persistent gas smell.
The condensate pipe isn’t frozen but the issue remains.
Error codes continue to appear.
There are unusual noises like banging or whistling.
To avoid future issues with your Worcester boiler, follow these preventative measures:
Schedule Annual Servicing – A Gas Safe engineer can identify and fix minor issues before they become major problems.
Keep the Condensate Pipe Insulated – Prevent freezing by insulating the pipe with lagging, especially in winter.
Check Your Gas Supply Regularly – Ensure your gas meter and supply are in good working order.
Monitor Boiler Pressure – Low pressure can impact performance; check your boiler’s manual for the correct pressure range.
Ensure Proper Ventilation – Make sure the flue is clear of debris and has adequate ventilation.
The cost of fixing a flashing blue light on a Worcester boiler depends on the underlying issue. Here’s a rough guide:
Resetting the boiler – Free (DIY fix)
Thawing a frozen condensate pipe – Free (DIY fix) or £50-£100 (engineer callout)
Replacing the flame sensor – £100-£250
Fixing ignition failure – £150-£300
Flue repairs – £150-£600
PCB replacement – £400-£600
Getting regular servicing can help you avoid costly repairs and extend the lifespan of your boiler.
A flashing blue light on your Worcester boiler isn’t something to ignore. While some issues can be resolved with a simple reset or thawing of a frozen pipe, others require professional attention. Keeping up with maintenance and servicing can help prevent these problems from occurring in the first place.
If you’re experiencing persistent boiler issues, don’t hesitate to contact a Gas Safe engineer to ensure your home stays warm and safe.
Search Should You Turn Your Boiler Off in Summer? Here’s the Truth. Summer’s here finally. The sun’s shining (most days),
Search Should I Upgrade My Central Heating System Before Winter? Winter in the UK can be brutal, with freezing mornings,
© 2024 Ignite Heating. All rights reserved